IBS 44:3. |
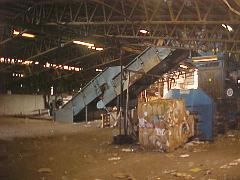 |
Presona Baler LP-100-DH/4 made 1995. Filling Opening: 2´050mm x 1´100mm. Capacity = 550 cubic meters pro hour. Capacity tons pro hour. Material 30 kg pro cubic meter = 16,5 tons. Material 50 kg pro cubic meter = 22 tons. Material 100 kg pro cubic meter = 32 tons Bale size: 1´100 x 750 mm x adj.length. Bale weights: 600 - 800 Kg. Wires: 5 Vertical. Press Force: 100 tons. Specific pressure: 12,2 Kp / cm² Max Oilpressure: 250 Bar. Oil tank Volume: 1´500 l. Electric Motors: 2 x 55 KW. Weight: 30 ton.
All above technical specifications are taken from Presona leaflets. |
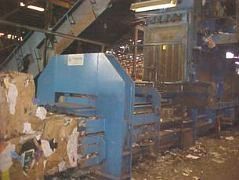 |
For a long time, LP-100-DH/4 balers were the biggest and most powerful balers Presona produced. This type of balers are equipped with a " Digging Operation ". This means if You overfill the baler with 10 - 20% too much material, the baler it self can " dig " out this problem. This " Digging Operation " is simple, and really good.
The Bottomplate on this Baler is worned and need to be changed.
|
|
26-07-2017. We are looking for one Buyer for this Baler who can buy and pick up the Baler during latest August - 2017. We are ready to accept a lower price, caused by the delivery date. It is only the Baler, No Conveyors are included. We sell the Baler including the lifting up to Lorries, but the Buyer shall have people with during the loading. Tom Eklund. +46 709 650 387
|
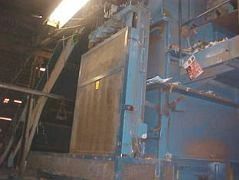 |
View over the tyingunit. 5 straight needles from the top operate the tyingunit.
Same owner since new. Just operated with clean paper.
Since this baler was new, Presona fitters from Sweden has made Service Visits twice a Year.
Those Contract Service Visits are Great, and gurantee that the Baler stay in very Good Condition.
|
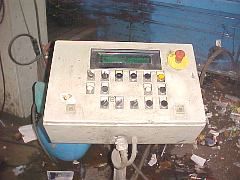 |
Picture over the Operation Panel.
This Baler is equipped with a program, original from Presona, to be able to change between 5 different " Working Programs " for the Baler.
Using a pressuretransmitter in the hydraulic system, allow us from this Operation Panel to set pressures in the different working programs.
Paper shall always been pressed by as high pressure as possible, plastic shall always be pressed with a lower pressure, not to destroy the wires. We can from this panel make different programs to match the material You wish to press.
This baler is also original equipped by a very good Fault Seeking System from Presona. If the baler stops working, You can read the reason for this stop in the Text Display.
|
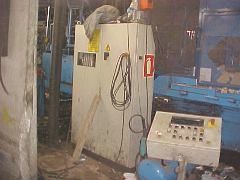 |
View over the Electric Cabinet and the Operation Panel. |
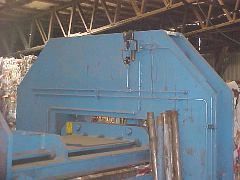 |
Directional valve in the front of the frictionchannel.
This is the valve which operate the output pressures for the materials.
This Baler is equipped with a program, original from Presona, to be able to change between 5 different " Working Programs " for the Baler.
Using a pressuretransmitter in the hydraulic system, allow us from the Operation Panel to set the pressures in the 5 different " Working Programs " for the baler.
This is really Good, and cooperate really good with Your needs for different settings for the different types from materials.
|
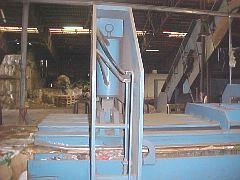 |
View over the front part of the baler.
The upper frictionflap is operated by 2 hydraulic cylinders.
Each of the side frictionflap is operated by 1 hydraulic cylinder, to be sure that we reach maximum pressure on the material.
|
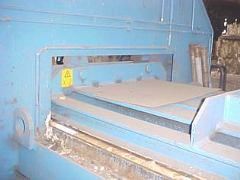 |
View over the front part of the baler.
The upper frictionflap is operated by 2 hydraulic cylinders.
Each of the side frictionflap is operated by 1 hydraulic cylinder, to be sure that we reach maximum pressure on the material.
|
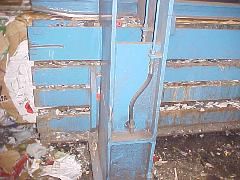 |
View over the front part of the baler.
The upper frictionflap is operated by 2 hydraulic cylinders.
Each of the side frictionflap is operated by 1 hydraulic cylinder, to be sure that we reach maximum pressure on the material.
|
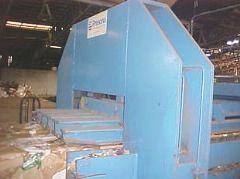 |
View over the front part of the baler.
The upper frictionflap is operated by 2 hydraulic cylinders.
Each of the side frictionflap is operated by 1 hydraulic cylinder, to be sure that we reach maximum pressure on the material.
|
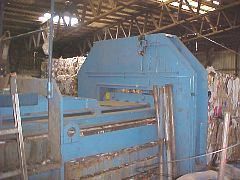 |
View over the front part of the baler.
The upper frictionflap is operated by 2 hydraulic cylinders.
Each of the side frictionflap is operated by 1 hydraulic cylinder, to be sure that we reach maximum pressure on the material.
|
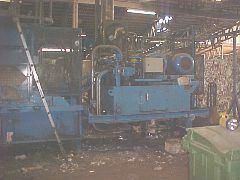 |
View over the Power Pac. |
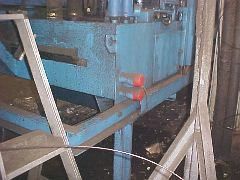 |
OPTION on this Baler.
Oil Heaters. |
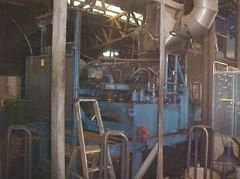 |
OPTION on this Baler.
Air Oilcooler. |
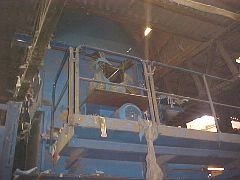 |
OPTION on this Baler.
Hydraulic operated Material Distributor.
This material distributor helps to make better bales from News and Magazines.
The propeller open up those types of materials. |
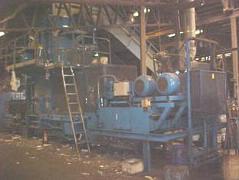 |
View over the Power Pac at the back of the Baler.
Loading Dimensions, and weights. Baler. Length: 10´350mm. Width: 2´270mm. Height: 2´680mm. Weight:30 trons.
Power Pac. Length: 2´800mm. Width: 2´300mm. Height: 2´520mm. ( If we dismantle the Air Oilcooler the height is: 1´620mm ). Weight:
Frame for Power Pac. Length: 2´750mm. Width: 2´700mm. Height: 140mm, ( made by 140mm U-Profil, 60mm wide ). Weight:
Materialdistributor. Length: 3´100mm. Width: 2´630mm, ( if we cut the inlet, the width is: 2´130mm ). Height: 2´300mm. Weight:
Wirepuller. Length: 2´950mm. Width: 1´350mm. Height: 365mm. Weight: 200 Kg.
Needle Frame. Length: 2´800mm. Width: 1´600mm. Height: 600mm. Weight:
Cover over Tyingunit. Length: 2´800mm. Width: 600mm. Height: 600mm. Weight:
2 Seperate Wireguides. 4 x Legs with a length from 2´820 mm, made from a U-100 profil. 2 x Upper Profils made from a U-100 profil, each with 5 Wire Guids. Total weight for those Wireguides: 400 Kg. At loading, when we have empty the channel from material, we can load those 2 Wireguides in to the channel.
Centers for the Wire Rolls, 10 Pcs. Length: 1´600mm. Width: 900mm Height: 900mm. Weight:
Electric Cabinet. Length: 2´200mm. Width: 1´200mm. Height: 420mm. Weight:
Balcony and Steps. Balcony around the top of the baler, with a seperate step included.
|
| | |
| | |